Insights
No matching resources. Please try a different filter
eBook
eBook
eBook
eBook
eBook
eBook
Article
Article
Article
Article
Article
Article
Webinar
Article
Webinar
Article
Webinar
Article
Article
Article
Article
Article
Article
Webinar
Webinar: Shifting from Dyne Solutions to Contact Angle Measurements
47:22 min to watch
Article
Article
Case Study
Article
Video
Article
Technical Paper
Article
Article
Article
Technical Paper
Article
Article
Webinar
Article
Article
Article
Article
Technical Paper
Article
Article
Article
Article
Webinar
Article
Article
Article
Article
Article
Article
Article
Article
Article
Webinar
Webinar: Top 3 Strategies to Improve Your Adhesive Bonding Operations
60.00 min to watch
Article
Article
Article
Webinar
Article
Video
Webinar: Creating a Digital Thread for Surface Preparation of Composites
60.00 min to watch
Article
Article
Article
Article
Article
Article
Webinar
Webinar
Article
Webinar
Article
Webinar
Article
Case Study
Webinar
Article
Article
Article
Article
Technical Paper
Webinar
Webinar
Webinar
Article
Video
Webinar
Webinar
Webinar
Webinar
Webinar
Webinar
Article
Technical Paper
Article
Webinar
Technical Paper
Technical Paper
Technical Paper
Webinar
Technical Paper
Webinar
Case Study
Technical Paper
Case Study
Case Study
Case Study
Webinar
Webinar
Technical Paper
Technical Paper
Technical Paper
Technical Paper
Technical Paper
Article
Article
Article
Article
Article
Brighton Science is
the global leader
in surface intelligence.
Tell us your goals or challenges, and we can advise you on specific solutions you can put to work immediately or build into your optimization processes.
What could this mean for you?
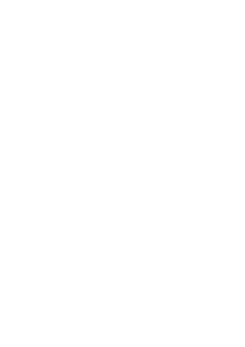